It all started in 1985 when Norman Peterson was employed as a workers’ compensation vocational counselor. One of his clients, Southwest Forest Products Plant #3, was experiencing a high incidence of injuries. Hardly a day went by without a call to the employer or a visit to the plant. Concerned about his employees’ well being, the company’s HR Manager, Dwayne Pont, was motivated to improve plant safety conditions. Despite numerous changes, injuries continued to occur.
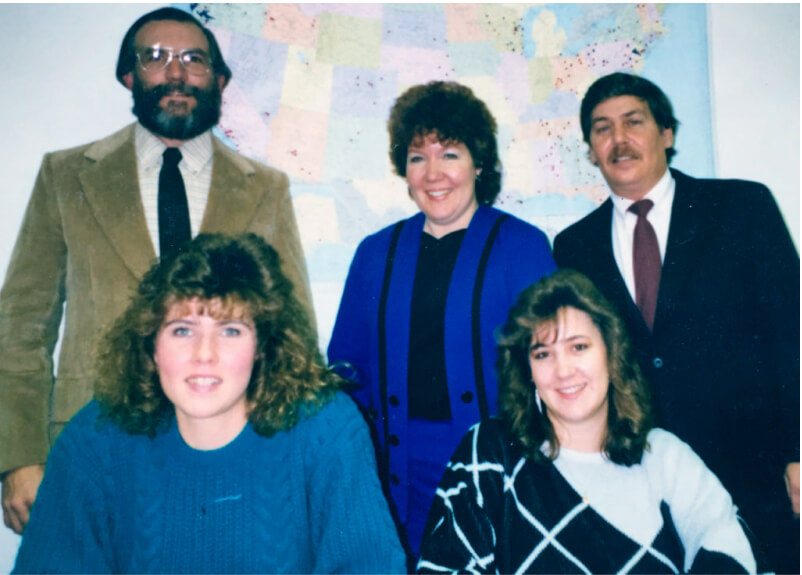
Some small descrition of the picture
Many mill workers off work for an extended time were participating in work hardening programs at rehabilitation centers that attempted to duplicate the actual work setting of the injured worker. Mr. Pont visited one of these centers to become more familiar with the work hardening process. When Mr. Pont saw his employees going through the motions of working at their old jobs, he realized there was no need for the rehabilitation center since he could just as easily provide his injured employees with work on site that approximated their regular jobs. After this visit, Mr. Pont challenged Norm to come up with a better way to help injured workers return to work while saving him time from the abundant paperwork involved in handling claims.
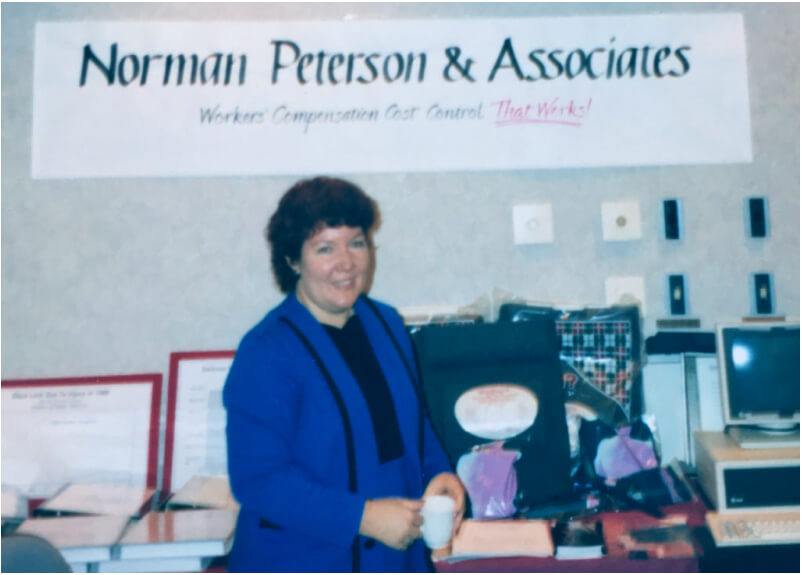
Some small descrition of the picture
Norm approached the problem using a systems analysis technique he learned while working at Lockheed. He realized that by analyzing the history of injuries, he could estimate how many, as well as what kind of, injuries were going to occur in the future. He matched these probable injuries with pre-planned tasks the worker could still perform after being injured.
Mr. Pont agreed with Norm’s analysis and contracted a number of temporary job descriptions. In the first year, workers’ compensation performance at Southwest Forest Products #3 went from being among the worst 100 mills in the United States to one of the top ten. Indemnity and medical savings were substantial. Due to these astounding results, both the mill and Norm Peterson received national attention.

Some small descrition of the picture
A matrix was developed which cross-referenced written available temporary job assignments with injured body parts and a range of physical capacities. This demystified and simplified the Return-to-Work process, allowing new employees, supervisors and doctors to quickly grasp and respond to the needs of individual injured workers. The temporary job assignments were called Bridge Assignments, to emphasize the healing process that occurs when a worker transitions from little or no physical capacities back to regular work.
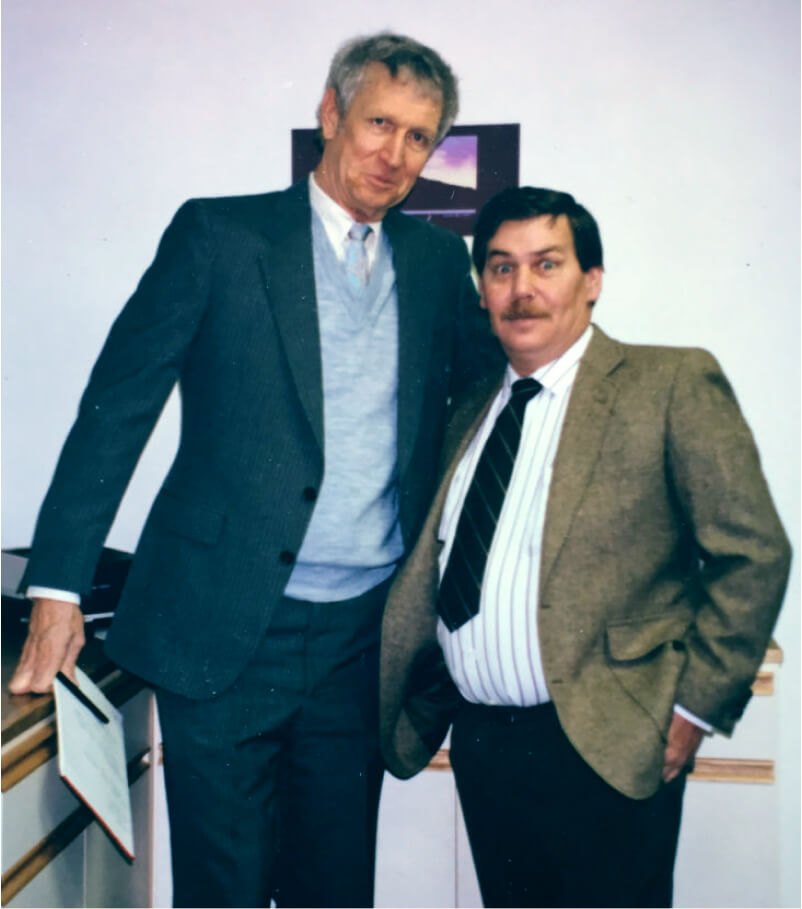
Some small descrition of the picture
Norm copyrighted the program as the OUR System® — Optimal Utilization of Resources. This name reflects his belief that 97% of injured workers prefer to be at work maintaining their productivity. NPA Norman Peterson and Associates (NPA) was incorporated in 1987. Since its establishment, NPA’s focus has been to help employers return injured workers to work as soon as they are physically able.
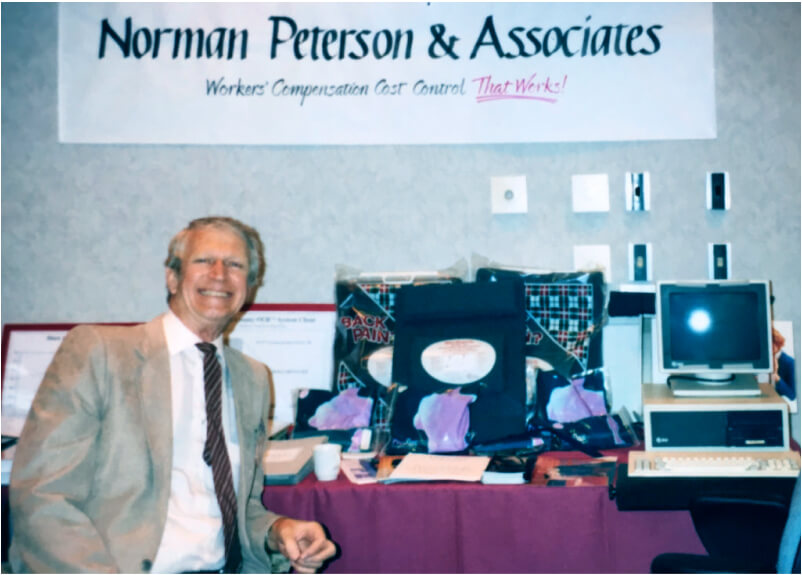
Some small descrition of the picture
Our Return-to-Work Specialists demonstrate how it’s a win-win-win proposition for employees, employers and doctors. NPA’s programs offer flexibility, including a variety of Return-To-Work services and financial arrangements. Our mission is to promote and implement the most effective, customized and straight-forward Return-to-Work system in the United States today.
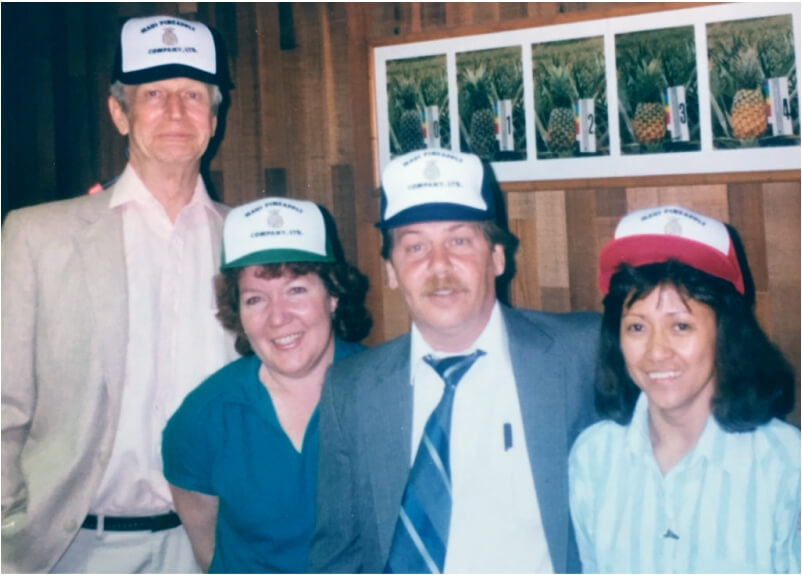
Some small descrition of the picture
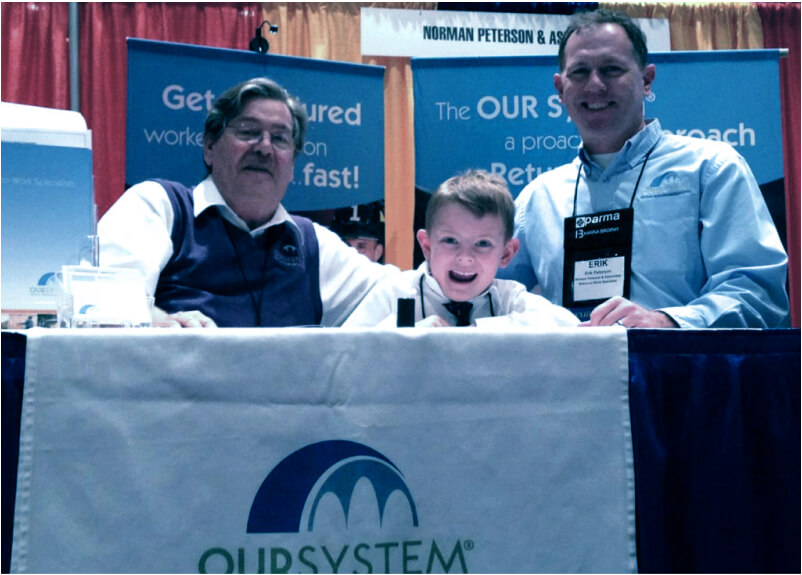
Some small descrition of the picture
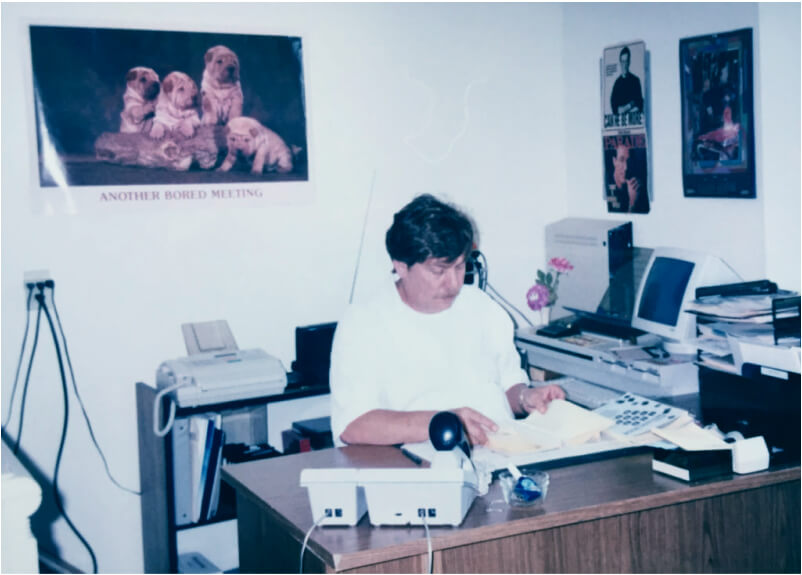
Some small descrition of the picture